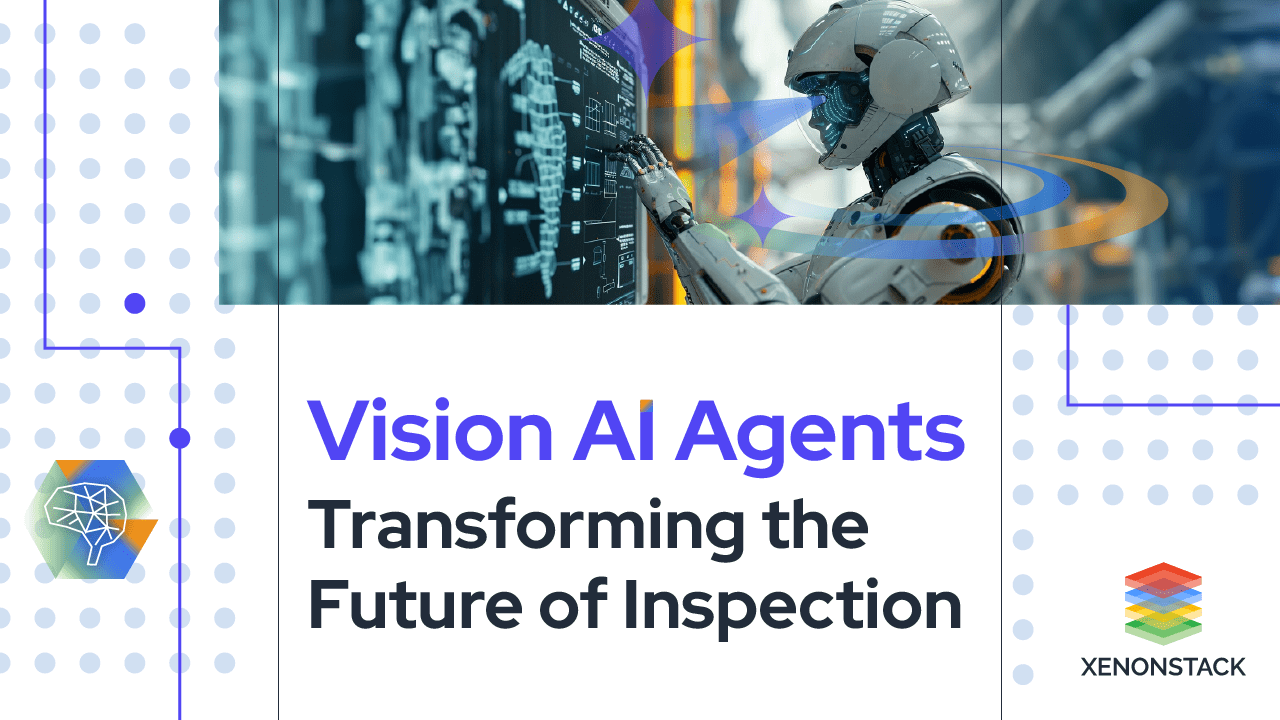
AI-Based Methodology
To develop an AI agent capable of identifying defects or differences in presented objects in real-time, the following steps would be involved: collecting relevant data, preprocessing the data, extracting features, developing a model, training the model, testing and validating the model, and finally deploying the model for real-time defect detection.
1. Commencing with Data Collection and Preprocessing: The process begins with gathering relevant visual data from the assembly line, including images or videos capturing various manufacturing stages. Subsequent preprocessing techniques refine and enhance data quality for optimal analysis conditions.
2. Annotating Data: During this stage, each dataset image or frame receives specific labeling, indicating defective areas, product types, or key features. Accurate annotation is crucial for training tools like Labeller, AWS SageMaker Ground Truth, or VGG Image Annotator (VIA).
3. Selecting and Designing Models: The crucial choice of model depends on the complexity of the task at hand. Various architectures, such as convolutional neural networks (CNNs) or recurrent neural networks (RNNs), are selected accordingly. The design of the model is customized to meet the specific requirements of assembly line inspection.
4. Training Models: Using the annotated dataset and selected model, training begins. The model learns to identify patterns and features within the data, with iterative parameter adjustments for accurate classification, detection, or segmentation.
5. Applying Augmentation Techniques: Augmentation improves model robustness and generalization. Variations like rotations, flips, or lighting changes are introduced in training data to prepare the model for diverse assembly line scenarios.
6. Validation and Testing: Trained models undergo validation and testing phases to gauge performance. Validation uses separate datasets to test generalization, while testing assesses real-world applicability in controlled environments.
7. Integrating and Deploying: Successful models integrate into assembly line systems, seamlessly linking computer vision with hardware and software components. Deployment ensures the model becomes an integral part of production processes.
8. Real-time Processing and Optimization: The final stage focuses on real-time application and refinement. The computer vision system operates continuously, analyzing assembly line data. Optimization includes fine-tuning based on real-world performance for consistent and reliable results.
Automated Inspection Workflow
-
Image Acquisition: As the incoming object approaches the system, it is detected by a sensor. Light sources and cameras influence the sensor’s input by lighting up the area and capturing an image of the object at exactly the right time. Successful image acquisition is necessary. Using the right optics and lighting techniques ensures high image quality. This is fundamental to carrying out an accurate and reliable analysis, which helps in quality control.
-
Image Processing and Analysis: The acquired image is pre-processed as technicians apply algorithms and several specific filters. They do so to detect the product in the image and highlight the key features of interest. Depending on the filtered image, you can use algorithms to generate a data object. This contains the characteristics of the inspected object’s highlighted features.
-
Result Evaluation: The software extracts data by comparing characteristics of the object’s highlighted key features with a predefined (that we have trained in the Model training phase) set of tolerances. These tolerances define the target quality level expected from the producer.
-
Decision Making: Subsequently, the system makes decisions based on the comparison between the processing results and the set tolerances defined in the model's training phase. It classifies the inspected object as passed or failed. Also, certain computer vision systems may be able to reject the product or trigger warnings, alarms, and similar actions.
-
Print Defect identification: In this phase, we detect anomalies in the prints like inconsistencies in color, text, or pattern. Manual inspection by human operators might lead to oversight that may lead to deterioration in quality. However, computer vision can perform print defect identification using AI. They do not miss out on any defects, especially the minor ones. Such technology benefits the production of prints, labels, and packaging prints.
Architecture of a Working System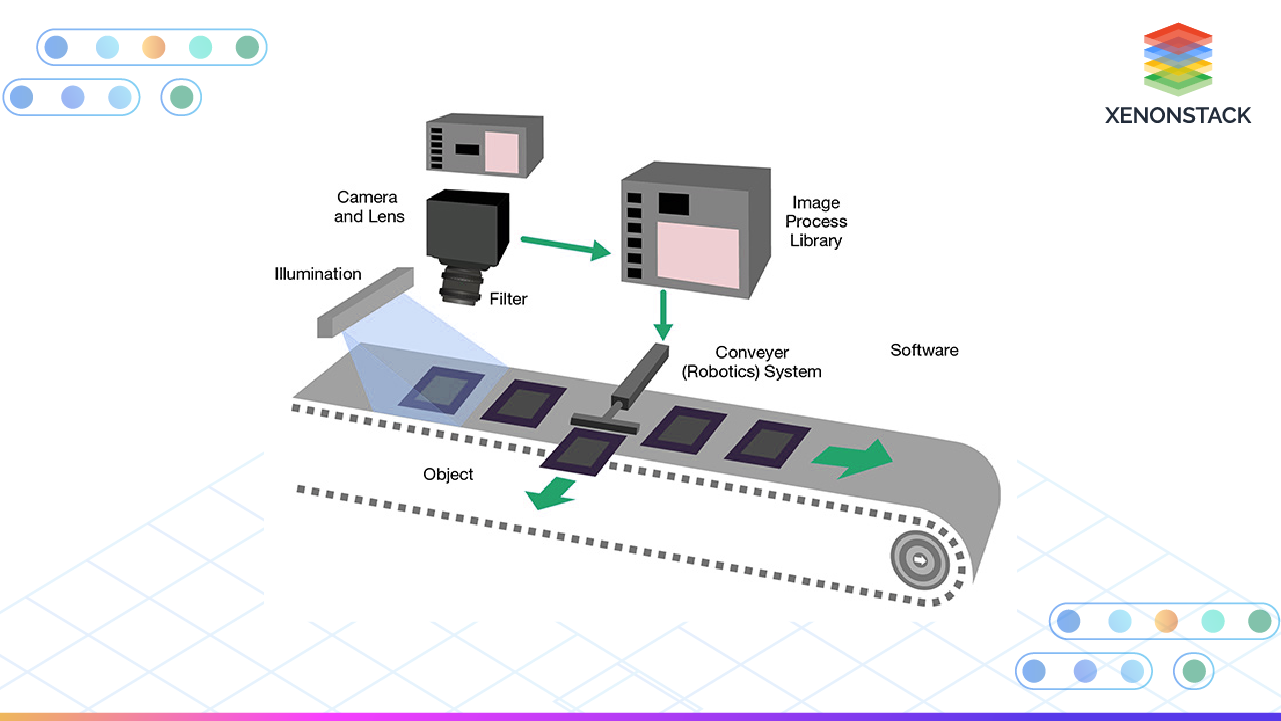
Now let’s see how the AI agent that we have trained, and tested that can identify defects or differentiations of any object can work with the combination of robotics
-
Camera and lens: A high-quality camera and lens setup are essential components of our defect detection system. The camera captures images of the objects passing through the inspection point. These images are then processed to enhance clarity and remove any distortions or imperfections. Proper illumination ensures optimal image quality, enabling the system to analyze and make decisions based on the visual data accurately.
-
Image Process Library (AI Agent) - The heart of our defect detection system lies in the AI agent, which is equipped with state-of-the-art image processing algorithms. Trained on a diverse dataset encompassing various types of defects and differences, the AI agent possesses the ability to discern even subtle deviations from the norm. Its decision-making process is driven by machine learning techniques, ensuring accuracy and reliability in defect identification.
-
Conveyer System – Acting as the interface between the AI agent and the physical production line, the conveyor system orchestrates the flow of objects based on the decisions made by the AI agent. Integrated with Arduino or Raspberry Pi technology, it translates the digital outputs from the AI agent into tangible actions within the manufacturing environment. By employing a lever mechanism, defective items are swiftly identified and diverted, ensuring that only flawless products proceed downstream for packaging or distribution.
Key Performance Insights
-
Image Acquisition Precision: High-quality image acquisition is pivotal for precise analysis and effective quality control.
-
Image Processing and Feature Extraction: Advanced algorithms and filters preprocess images, highlighting crucial features for accurate object detection.
-
Outcome Assessment and Decision Making: Processed data undergoes meticulous evaluation against predefined standards, facilitating object classification and initiating actions based on comparison outcomes.
-
Production Process Optimization: Computer vision systems utilize inspection data to identify production trends and offer tailored recommendations for process enhancement.
-
Focused Object Detection: The AI agent adeptly identifies and isolates individual objects within images, streamlining tasks such as sorting and quality assurance.
-
Print Defect Detection: The AI agent meticulously identifies inconsistencies in prints, ensuring thorough inspection and enhancing overall print quality.
Benefits of Vision Agents
-
Increased Accuracy and Consistency: Vision Agents offers high levels of accuracy and consistency in inspection tasks, minimizing the risk of human error. Studies have shown that implementing this can reduce error rates in inspection processes by up to 90%.
-
Enhanced Efficiency and Productivity: Automating inspection tasks with vision agents reduces inspection times and increases throughput, enhancing overall productivity. Research indicates that using this and robotics in manufacturing can increase productivity by up to 30%.
-
Cost Savings: Vision agents help companies save on labor costs and avoid expensive rework or product recalls by minimizing the need for manual labor and reducing errors. Companies using vision agents report an average ROI of 6 months to 1 year.
-
Improved Quality Control: Vision agents enable thorough and consistent inspection of products, ensuring adherence to quality standards and specifications. Driven by the growing emphasis on quality control across various industries, the anticipated market size for global computer vision inspection is projected to reach USD 17.9 billion by 2027.
The adoption of Vision Agent offers many benefits for inspection and assessment processes across industries. By leveraging advanced algorithms and automated systems, computer vision enhances accuracy, consistency, and efficiency in inspection tasks, leading to improved productivity and cost savings. Furthermore, computer vision enables thorough quality control, ensuring adherence to standards and specifications while minimizing the risk of errors and defects. Real-time monitoring capabilities empower proactive decision-making and facilitate timely intervention, thereby reducing downtime and enhancing overall operational efficiency.
As organizations continue to embrace computer vision solutions, they stand to gain a competitive edge through optimized production processes, enhanced product quality, and streamlined inspection workflows. With the global computer vision market poised for substantial growth, the future promises even greater advancements in inspection and assessment technology, driving innovation and transformation across diverse sectors.